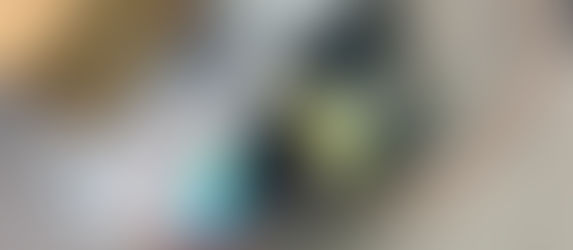
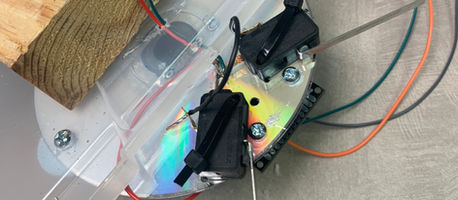
Telepresence Robot
I live in Boston and my family lives in Utah. I have been looking for a fun project to do, and so I decided to make a telepresence robot....


Sheet Metal Rose
Passionate and elegant but made of strong stuff. My grandma loves roses. She has a giant garden full of flowers and I'd always help her...